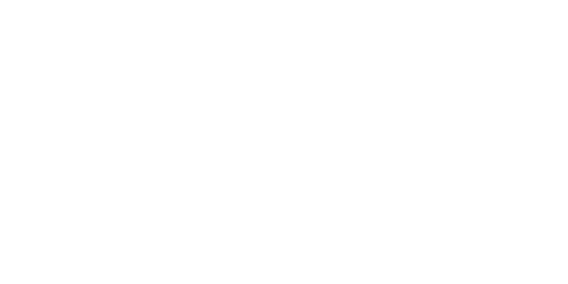
A Tip from an Expert: CAN FD vs. CAN Classic –
More Speed, more Future – Time for CAN FD?
Requirements are increasing, as are data volumes – time to switch from CAN Classic to CAN FD.
In many industrial applications CAN (Controller Area Network) has been the standard for decades β robust, cost-efficient and reliable. But the world is changing: machines are becoming more networked, data volumes are increasing, and response times are becoming more critical. Those who still rely on CAN Classic today risk reaching their limits tomorrow.
The solution: CAN FD (Flexible Data Rate) β the logical successor that sets new standards in efficiency and speed. But why is CAN FD not yet being used consistently in many projects? And why is it no longer worth putting off the changeover?
What is CAN FD β and what is the difference to CAN Classic?
CAN FD was introduced in 2012 by CiA (CAN in Automation) as a further development of CAN Classic. The most important differences:
πΉ larger user data fields: instead of 8 bytes, up to 64 bytes per frame are possible
πΉ higher data rates: up to 8 Mbit/s β instead of 1 Mbit/s with CAN Classic
πΉ more flexible & efficient: less overhead, better bus utilisation
This means: more information, in less time, with the same robustness.
Typical applicatons for CAN FD
CAN FD is particularly useful where:
β
several sensors communicate simultaneously
β
diagnostic data or firmware updates are transmitted
β
mobile maschinen, vehicles or test systems work with increasing data requirements
β
a future-proof basis is to be created for later system expansion
Example: In modern agricultural or construction machinery, CAN FD enables the parallel data transfer of hydraulic sensors, GPS modules and engine controls – without bottlenecks in the bus.
Why many are still waiting to make the switch
Hesitant introduction is often due to:
- concerns about compatibility problems with existing CAN Classic components
- lack of implementation expertise
- lack of resources for protocol development
But the transition can be organised smoothly – with the right partner at your side.
How MicroControl supports you on the way to CAN FD
As a long-standing member of CiA and specialist in CAN communication, MicroControl offers:
β
protocol stacks, which support CAN Classic as well as CAN FD
β
modular solutions, which can be seamlessly integrated into existing systems
β
consulting and support from experienced developers
β
proven tools for rapid implementation
Our stacks save you development time – while ensuring technological sovereignty for years to come.
Conclusion: Those who opt for CAN FD today will save twice as much tomorrow!
β
more power
β
more data
β
more future-proofness
The technology is there. The standards are established. The advantages are obvious. Now is the right time to take the next step.
CANopen, CANopen FD and J1939 protocol stacks are set for the future and offer the possibility to migrate from CAN Classic to CAN FD at any time.
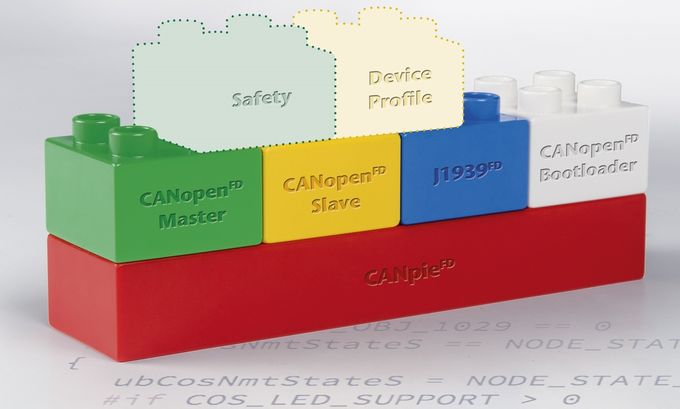