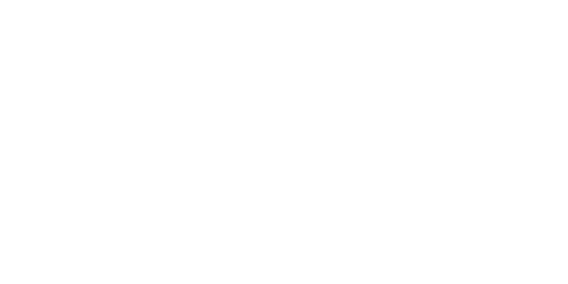
The CiA (CAN in Automation) –
Meticulous Search for the Best Standards
The origins of the CAN bus protocol (Controller Area Network) extend far back in the past – even before automation and digital transformation became an issue. Bosch already laid the foundation for the bus system in 1986 to enable electronic communication between the upcoming control units, sensors and actuators which were increasingly used in cars at that time. Manufacturers started to include active suspension systems, gear and light control, central door locking and ABS. To enable interaction between different electronic units, to exchange data and to perform tasks correctly, a new and easy-to-use bus system was needed. This was when CAN came into existence which, right from the start, was considered to be a simple, secure and efficient solution.
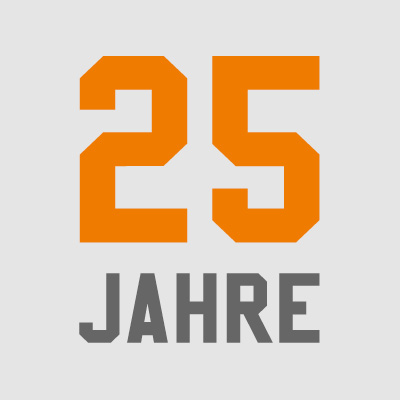
Required: easy, reliable, secure
Requirements were clearly stipulated: the bus system had to work reliably in vehicles in any kind of condition imaginable. Simple wiring, high security in data transmission and a rugged and clear structure were relevant features at the time – features which, in the meantime have also become important in many other kinds of application: the CAN protocol facilitates simple wiring as the electronic devices can communicate through a single multiplex line which connects each node in the network. The multiplex architecture enables combination and transmission of signals in the entire network through a single line, so that each electronic module gets the data from sensors and actuators at the right time.
Standardization as motor
The CAN protocol was standardized by the International Standards Organization (ISO) in 1993. A year before, experts founded the CiA user organization to standardize the CAN bus and to simplify implementation in different applications. “To be able to use the CAN bus in applications of different industrial areas, standardization was inevitable”, explains Uwe Koppe, MicroControl CEO and technical director of the CiA. “Identical protocols simplify handling of every system.“ In the past 30 years, the CiA has issued more then 20,000 pages with specifications.
The CAN protocol was standardized by the International Standards Organization (ISO) in 1993. A year before, experts founded the CiA user organization to standardize the CAN bus and to simplify implementation in different applications. “To be able to use the CAN bus in applications of different industrial areas, standardization was inevitable”, explains Uwe Koppe, MicroControl CEO and technical director of the CiA. “Identical protocols simplify handling of every system.“ In the past 30 years, the CiA has issued more then 20,000 pages with specifications.
The future has just begun
CAN bus will be the future technology: Introduced in 2012, CANopen FD defines the next level of development: FD stands for Flexible Data rate and marks the progress in development of the data protocol to be able to process higher date rates. To facilitate migration to FD, MicroControl systems are equipped with the possibility to switch from CANopen to CANopen FD. “As technological leader and CiA member we are always at the pulse of time”, says MicroControl head of sales, Frank Wielpütz. “Our modules have been equipped with the possibility to switch from CANopen to CANopen FD for years. So, our customers have the possibility to switch over in future projects.“
A new option is the CAN XL protocol which is currently in the release procedure. With its high transfer rates the CAN XL closes the gap between CAN and Ethernet, but will continue to feature small, economic and fail-safe modules. CAN networks in IoT devices, in automation, in satellites and space vehicles on their way to Mars – many things are possible in the CAN future.
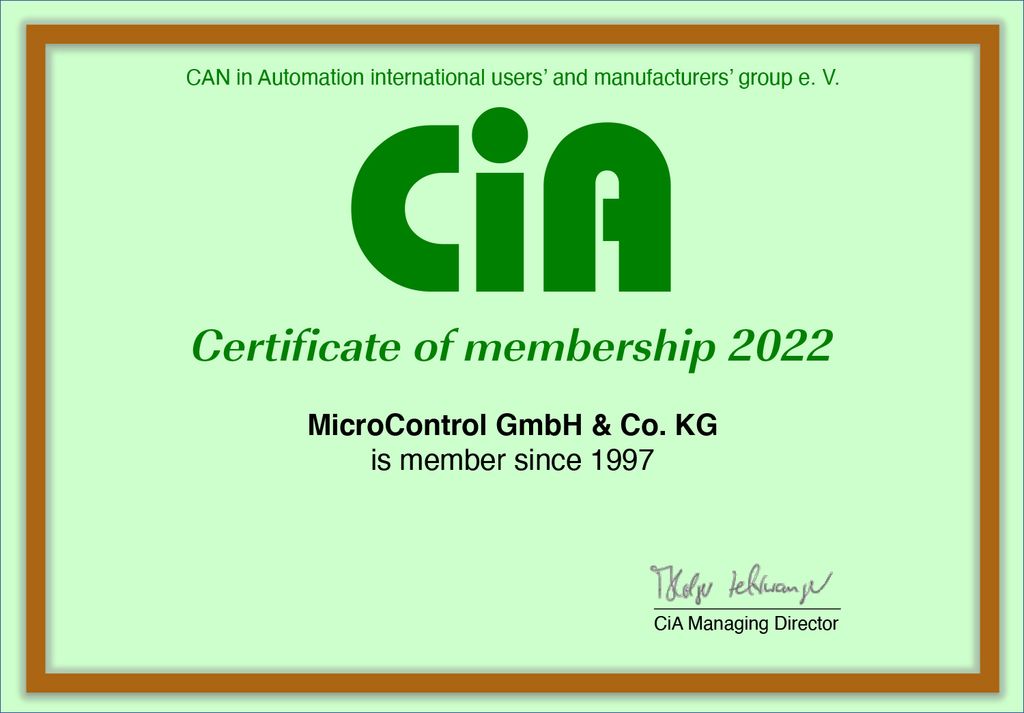